Strategic partner: Boeing
The future of
flying
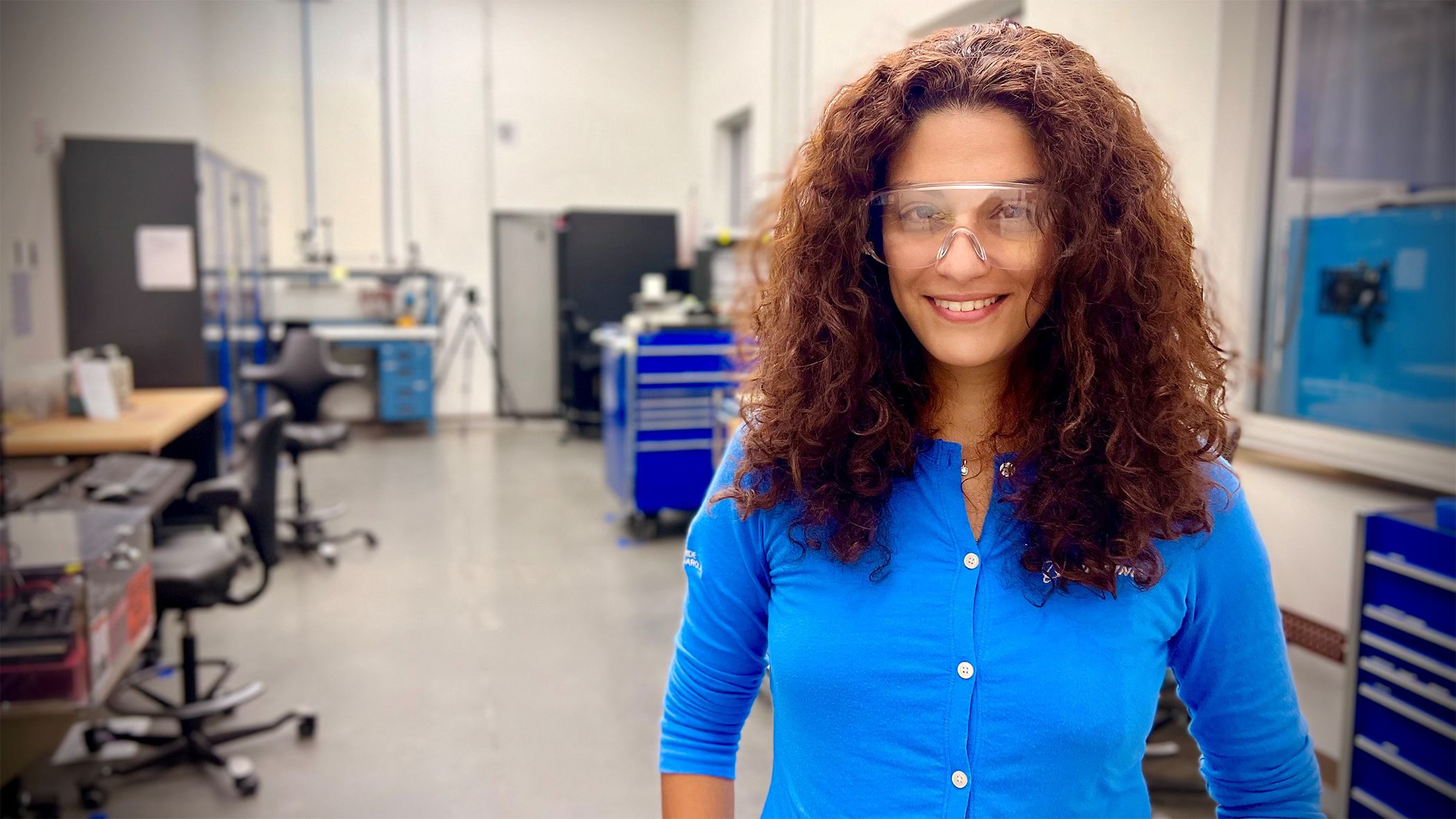
To make aviation climate neutral is an urgent but hugely complex and multi-faceted task. It requires breakthroughs in fundamental science, the development of new technologies and changes to the way the whole industry works.
University of Cambridge and Boeing research teams have worked closely together for nearly 20 years, asking difficult questions and seeking solutions to some very complicated problems.
Taking the sector to net zero is arguably the most complicated problem of all, which will need "commitment, collaboration and intense research focus to get us to where we need to be," says Ellen Ebner, Director of Sustainability & Future Mobility at Boeing.
"Boeing's partnership with the University of Cambridge is central to the effort of making aviation carbon neutral.
As well as helping us to find technology solutions, it is bringing together academic and industry partners to drive change at the 'system' level. We need to work as a sector, and Cambridge is playing a pivotal role in making that happen."
- Ellen Ebner, Director of Sustainability & Future Mobility, Boeing
This remarkable partnership asks difficult questions from how do you change a whole sector to what will the green aircraft of the future look like?
And it takes us to some unexpected places: ice sheets, intensive care and the invention of 'ghost' cars.
All this - and a Guinness world record to boot - shows the power of blue-sky thinking and why industry-academic collaborations can be so successful.
20 years of
CAMBRIDGE & BOEING
Research partners since 2003
Working with the Departments of
Engineering, Computer Science and Technology, Materials Science & Metallurgy, Physics, Sociology and the Scott Polar Research Institute
Boeing is also an Aviation Impact Accelerator partner
Together we are addressing topics such as
transitioning the aviation sector to net zero, electric and hybrid-electric propulsion, advanced materials and manufacturing technologies, human-computer interaction and managing disruption.
Unlocking sustainable aviation
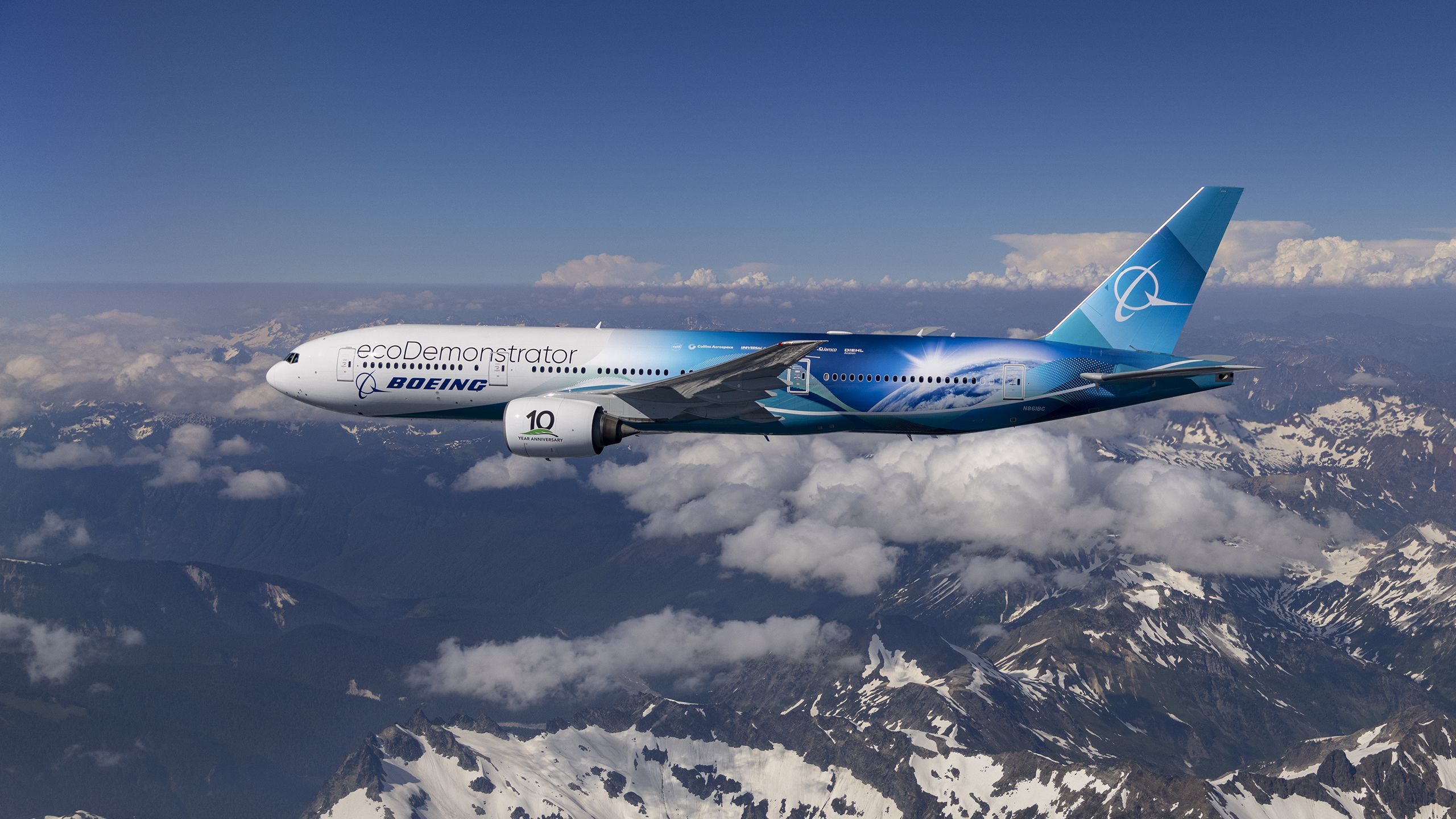
In 2019 Boeing took part in a roundtable discussion at Cambridge alongside other major players in the aviation industry, chaired by His Majesty, King Charles. They were there to talk about sustainable aviation and how to make it happen.
The Aviation Impact Accelerator (AIA) was born, and Boeing has come on board as one of three major industry partners, with Rolls-Royce and Etihad Airways. Since then, the AIA has built a model from which tools and insights can be developed that allow people to map, understand and embark on the pathways towards sustainable aviation.
Its first tool is the Resource to Climate Comparison Evaluator (RECCE). This can be used to compare different aviation fuels, their impact on the climate, the resources they use and their costs.
The AIA has also published a report, in collaboration with the World Economic Forum, examining the technical capabilities of battery-electric, hydrogen fuel cell and hydrogen combustion aircraft and the role they might play in accelerating the aviation sector to true zero.
"What we are trying to do with the AIA and by working with partners like Boeing, is to identify system 'unlocks'," says Professor Rob Miller, Director of the Whittle Laboratory in Cambridge. "Bottom-up modelling can help us identify possible unlocks and can cut through complexity to open doors to much wider transformations.”
"Boeing has been involved in the AIA from the start," explains its manager, Beth Barker, "providing expertise in developing and troubleshooting our aircraft modelling and in evaluating some of our other industry models."
For Neil Titchener, who has been leading Boeing’s involvement in the AIA, “being in an open forum with stakeholders from across the whole aviation sector will allow us to trailblaze this path to net zero."
"We’ve been able to contribute our expertise particularly around aircraft modelling and we have also been able to learn from the work going on around sustainable aviation fuels which will obviously have a huge part to play in the future of the industry.”
Electric dreams
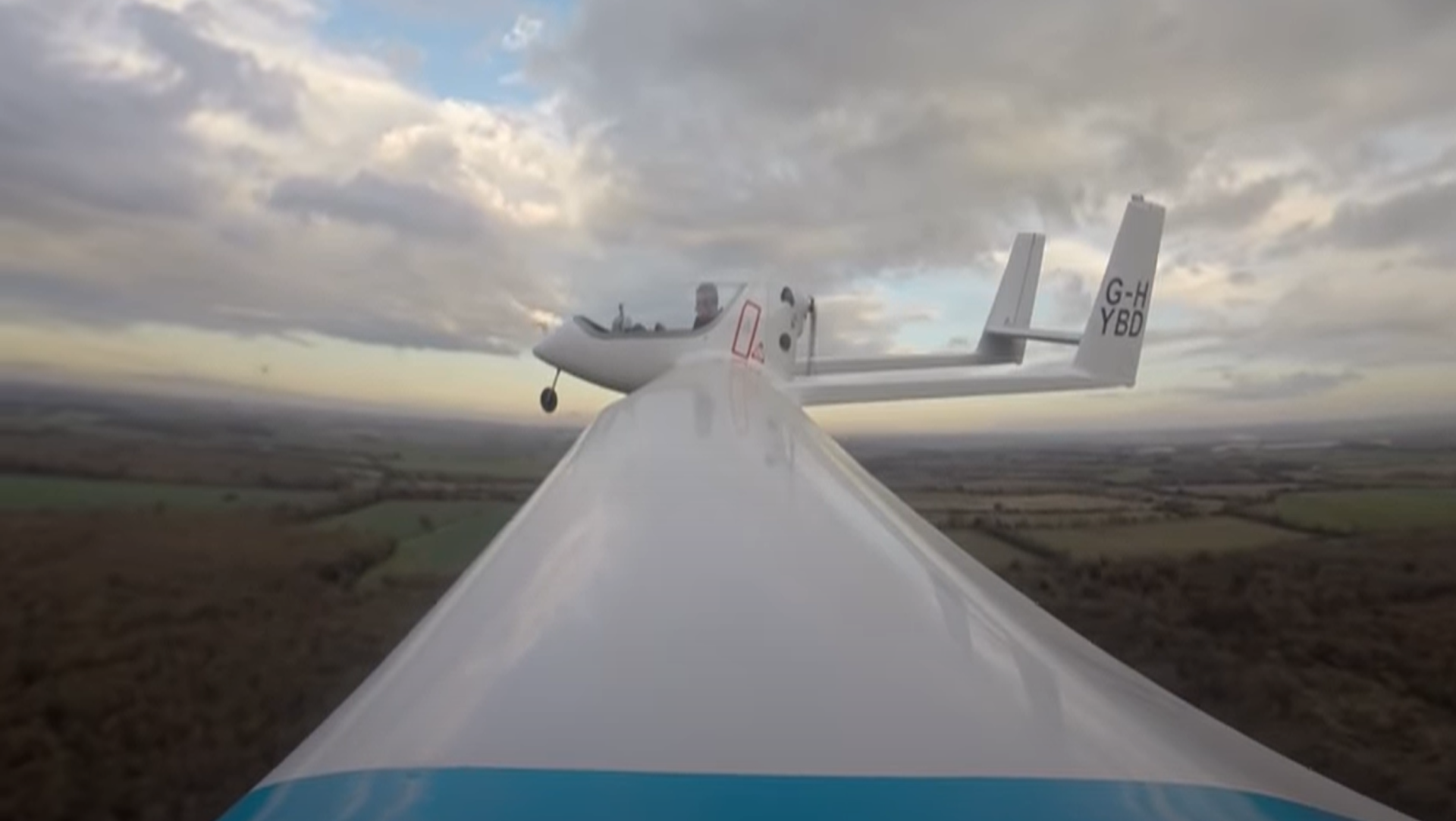
One of the ways in which aviation can be made more sustainable is through the development of electric aircraft.
However, according to Professor Paul Robertson from Cambridge’s Department of Engineering, it will be a long time before dreams of fully electric, long-haul passenger aircraft become a commercial reality.
"The limiting factor is battery technology. We are decades away from having a battery that can store sufficient energy for a long-haul flight while being light enough for a plane to get off the ground."
But hybrid-electric planes are a much nearer term proposition for aircraft manufacturers, with a number of models close to commercial deployment. The benefits, explains Robertson, are that they use less fuel and create fewer emissions than a conventional aircraft. They do this by using a combination of fuel and electricity to provide the power needed for take-off and climbing then switch to much more efficient fuel-only engines when cruising along at a steady speed.
In 2014, Robertson and his team worked with Boeing to develop a single-seater demonstrator which used up to 30% less fuel than a comparable plane with a petrol-only engine - and was able to recharge its batteries in flight.
Robertson explains: "Until someone invents the magic battery, hybrid planes - particularly for light aircraft - will be a useful transitioning technology, allowing us to significantly increase fuel efficiency and, in time, we will be able to combine electric with sustainable aviation fuels, further reducing their carbon footprint."
For Robertson, working with Boeing has been a productive experience. "Because these aircraft have to work in the real world, Boeing placed serious design constraints on us. But as academics, that gives us something positive to aim for. Boeing tells us what they need in the application space, we apply our design and innovation skills and together we see what comes out."
Reimagining flight
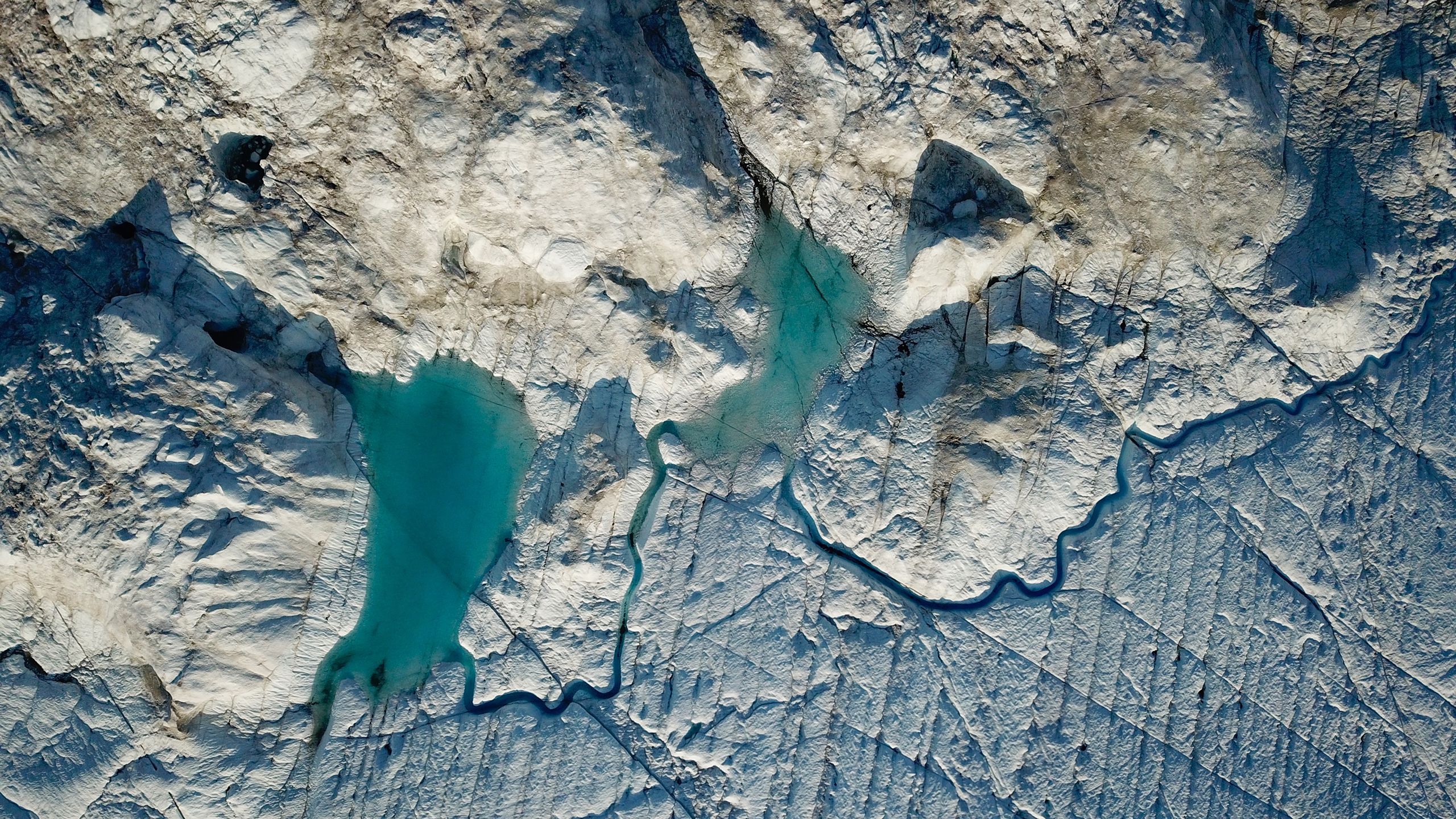
Robertson is not the only Cambridge engineer working with Boeing on hybrid-electric planes. It was through a research project on melting glaciers that Professor Jerome Jarrett and his team found themselves drawn into this challenge.
Cambridge scientists from the Scott Polar Research Institute (SPRI) are trying to get a better understanding of how an increasing amount of meltwater is altering the behaviour of the Greenland ice sheet's large outflow glaciers.
"We needed to search for meltwater pools on the glacier in order to observe them for an extended period of time," explains Jarrett. "Satellite overflights were too infrequent to capture the daily changes the SPRI team were interested in. Trying to operate from field stations on the ice, far from runways, would require vertical take-off, but helicopters are expensive and involve putting human crews into a potentially hostile environment."
A standard four-rotor style drone couldn't carry the weight of the commercial mapping technology the SPRI team wanted to use for anything like the required mission length. What was needed was an aircraft that was light enough for two people to carry, able to take off vertically and then fly conventionally for several hours, mapping around 1,500 square kilometres of ice before returning to its launch point.
Jarrett and team opted for a design using tiltable propellers, a configuration that would make hybrid-electric propulsion an attractive choice. Phantom Works, with its interest in this field, came on board and, having successfully developed the concept for an unmanned aerial vehicle (UAV), Jarrett's team is now working with Boeing on the next step: applying this hybrid design optimisation approach to the 20-seater market.
But this ambitious project aims to do more than design a viable hybrid. It is about going back to first principles to reimagine what an aircraft looks like.
Jarrett says: "If you ask someone to draw an airplane, it is likely to have a tubular fuselage, swept wings and a tail because that's what commercial planes have looked like for the last 60 years. That configuration has been determined by the use of kerosene-fuelled jet propulsion. But change the way you power the plane, for example, by switching to hydrogen and/or electricity, and all the assumptions built into design rules assuming kerosene fuel no longer hold."
Jarrett's team is developing a set of computational approaches for configuration optimisation that will free aerospace engineers from the constraints imposed by using fossil fuels, opening up the design space for the greener aircraft concepts of tomorrow.
“A system that can explore large changes in airplane configuration can accelerate development, adapting to changes in missions and technologies needed for greener aviation.
Cambridge is showing the capabilities and benefits of a design system that can reimagine the airplane."
- Sean Wakayama, Boeing Principal Investigator
Superconductivity
for electric planes

Batteries are not the only obstacle to electric, long-haul aviation. Another challenge is building an electric motor that is powerful enough to fly the plane while being small enough that it can get off the ground.
To help solve this problem, Boeing and Cambridge have been working together on bulk superconductivity for more than 15 years. Their ultimate aim is to be able to switch to superconducting generators and motors in order to make an electric plane that is light enough to fly.
In 2014 their efforts were rewarded with one of the world’s most sought-after accolades: an official Guinness World Record, for the strongest magnetic field trapped in a bulk superconductor.
Leader of the Bulk Superconductivity Group, Professor John Durrell and his team at the Department of Engineering are looking at the underlying technological challenges. Durrell explained: “If you want to have a large magnetic coil made out of superconductors, you need to be able to set the magnetic field up in a reliable and robust way. Key to that is being able to connect superconductors together without introducing too much resistance.”
"This is an important enabling technology that’s still in the future. It’s taking the physics of superconductors and deploying good science and engineering to turn them into practical realities.
There are obvious constraints in our way, such as the need for cryogenic cooling, but breakthroughs in superconductivity could help us make a transformative leap in efficiency which would be critical if we are to achieve our vision of creating zero environmental impact."
- Pat Stokes, Boeing Executive Focal and Research Portfolio Leader for the University of Cambridge.
The physics of flying
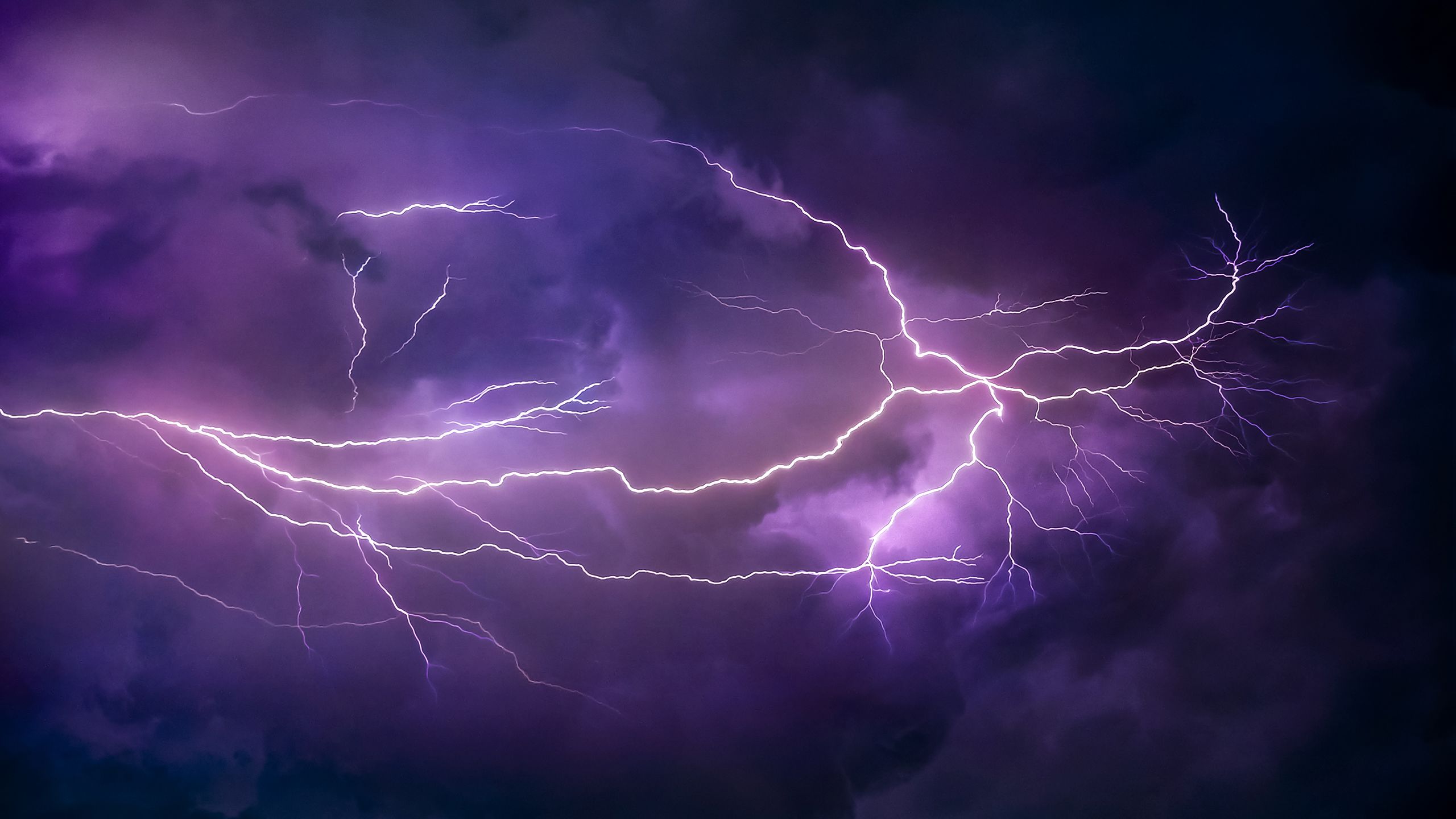
"Finding new ways to operate more efficiently is also an important part of our commitment to meeting our decarbonisation targets," says Pat Stokes, Boeing Executive Focal and Research Portfolio Leader for the University of Cambridge.
"Addressing how we manufacture our aircraft and manage our operations is helping us take incremental but significant steps in reducing our environmental impact."
Complex physics and mathematical modelling have been helping Boeing tackle some of these real-world operational challenges, including how to de-ice aircraft wings more sustainably, how to mitigate lightning strikes, and how to 3D print complex parts more effectively and accurately.
The Laboratory for Scientific Computing, led by Professor Nikos Nikiforakis, is pioneering this novel approach. By combining physics with applied maths and high-performance computing, the team is able to model highly complex scenarios, such as how different states of matter (whether plasma, gas, solid or liquid) behave at a macroscopic level when they interact.
De-icing wings
To ensure planes are safe to fly in what are called icing conditions (that is, when ice is likely to form on a plane), wings and engine inlets must be kept ice-free at all times throughout the flight.
Today, for both large aircraft and small, this is achieved using a variety of methods: heaters, pneumatic ducting, fluids that lower the freezing point of water or inflatable rubber 'boots' which expand to break off any accumulating ice. The objective of the Cambridge research was to evaluate a more effective and more energy-efficient way of doing it.
Nikiforakis and his team have applied their computational multiphysics methods to see if, by creating tiny vibrations using ultrasonic transducers placed under the skin of an aircraft, it is possible to stop ice formation.
No commercially available software has all the underlying physics necessary to accurately simulate this phenomenon at the macroscopic level, so the team built a bespoke multiphysics algorithm which has successfully revealed the underlying physics of this process and has demonstrated its effectiveness in a real-world scenario. The next step is to take these findings and test them in Boeing’s icing tunnels.
When lightning strikes
On average, commercial planes are hit by lightning once a year. While they are designed to withstand these strikes, every time they happen, the plane may be temporarily taken out of service while it as assessed for damage and any repairs carried out. This can cause significant disruption to schedules which, in turn, contributes to inefficiencies.
By understanding the physics of a lightning strike and how it affects the different materials in a plane, this research is helping Boeing rethink how parts are designed, what damage limits are recommended for particular components and how maintenance and repair practices should evolve accordingly.
One of the Boeing team members carrying out this research is Cambridge PhD, Louisa Michael, who was a postdoctoral researcher in Nikiforakis's Scientific Computing Laboratory.
“In spite of the importance of the topic, there’s only a small part of the world focused on lightning and aviation research, and an even smaller subset falling in the intersection between academia and industry where innovative technology finds its way into industrial applications,” Michael says. “It’s fascinating to work on such complex but very real problems.
"I get to collaborate with other people around the world who share my expertise in this area," she continued. "And all this would have not been possible without the very talented Cambridge research team and my exceptional Boeing EME teammates. It’s pretty exciting to see all of that coming together.”
Nikiforakis adds: "There is no other model in the world that can capture the two-way interaction between lightning and a material, so this is a very significant advance both in fundamental mathematical physics and in terms of numerical analysis and scientific computing."
Printing parts
As aircraft design changes to benefit from new, more sustainable technologies, manufacturers like Boeing are increasingly turning to 3D printing to produce the large, complicated components these new designs demand.
3D printing (or additive manufacturing), is also more efficient and creates less waste than conventional manufacturing.
Melting the metal powders used for 3D printing is a multiphysics problem and therefore of interest to Nikiforakis and team. Understanding what's going on as the powder becomes a liquid and then cools to become a new solid - and being able to model that process mathematically - can help us to better understand the properties of the finished part, and to improve the techniques used for additive manufacturing.
Nikiforakis explains why this is important: "Commercial software packages are available to address this issue. However, not only is our computational model an order of magnitude faster than any currently on the market, it can also simulate innovative manufacturing processes developed at the University's Institute for Manufacturing using an array of lasers."
For Boeing's Pat Stokes, this multiphysics approach, "is very exciting work and highlights the importance and value unleashed via the development and utilisation of model-based engineering and simulations of highly complex physics phenomena."
Where people and computers meet
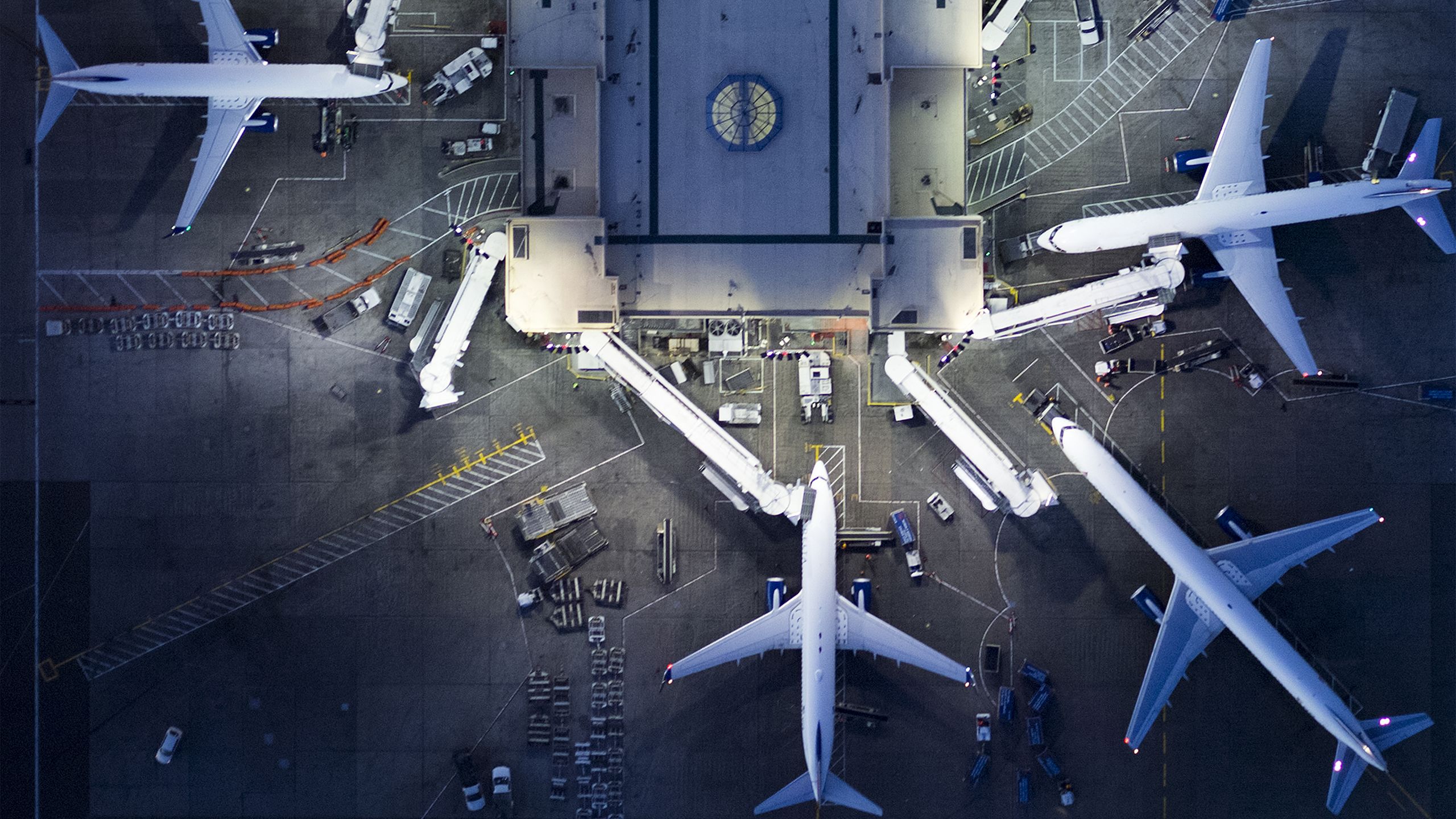
"My part of the Boeing portfolio is the most cross-disciplinary, often involving PhD students with backgrounds in the social sciences, psychology or business," says Professor Alan Blackwell, from the Department of Computer Science and Technology. "That's because my group tends to get involved in projects where humans and technology are coming together in a way that creates some kind of issue."
For example, if you were to have a maintenance manual for a 747 it would be so huge you would, says Blackwell, "need a van to drive it around". The question Boeing asked Blackwell and his team was 'how you can design computer systems, including screens and keyboards, that make it easy to find the information you need when you are in the middle of doing something very complicated?'
Boeing funded a PhD student with a background in the anthropology of dance to investigate this challenge. But, as Blackwell explains, "for this kind of work you have to go into an organisation and watch how people set about their tasks. Boeing factories are not places where you can have research students wandering around, so we looked for another domain - a bit closer to home - with a similar set of problems."
They found the ideal location, a place where teams of people work together in a complex situation and need to access data: the Royal Papworth Hospital in Cambridge.
The student observed the transition in the intensive care unit from paper notes to an electronic patient record system with a screen at the end of each bed. Her background in anthropology and dance enabled her to study the way that the anaesthetists, consultants and the nursing team were 'choreographing' their work by adjusting the positions of their bodies relative to the patient when the computer was introduced.
Paths not taken
Blackwell's team has also been investigating situations where human decision-makers and AI agents are interacting with one another and forming ideas about what each other is thinking.
To do this, they built a prototype which looks at how autonomous vehicles in a city interact with human drivers.
Blackwell explains: "We came up with a way of visualising the basis on which they're making decisions and playing out scenarios. It allowed us to look simultaneously at many possible universes in which different things might happen depending on the decision that you take. All those different universes are represented in our model by 'ghost cars' driving around."
"This technology will have an impact in the future when, for improved safety and efficiency, we will have airplanes that can taxi and relocate autonomously at busy airports, fully aware of their location, perceiving and negotiating with the other vehicles such as airplanes and ground vehicles.”
- Dr Dragos D. Margineantu, Boeing Senior Technical Fellow, AI Chief Technologist
Managing disruption
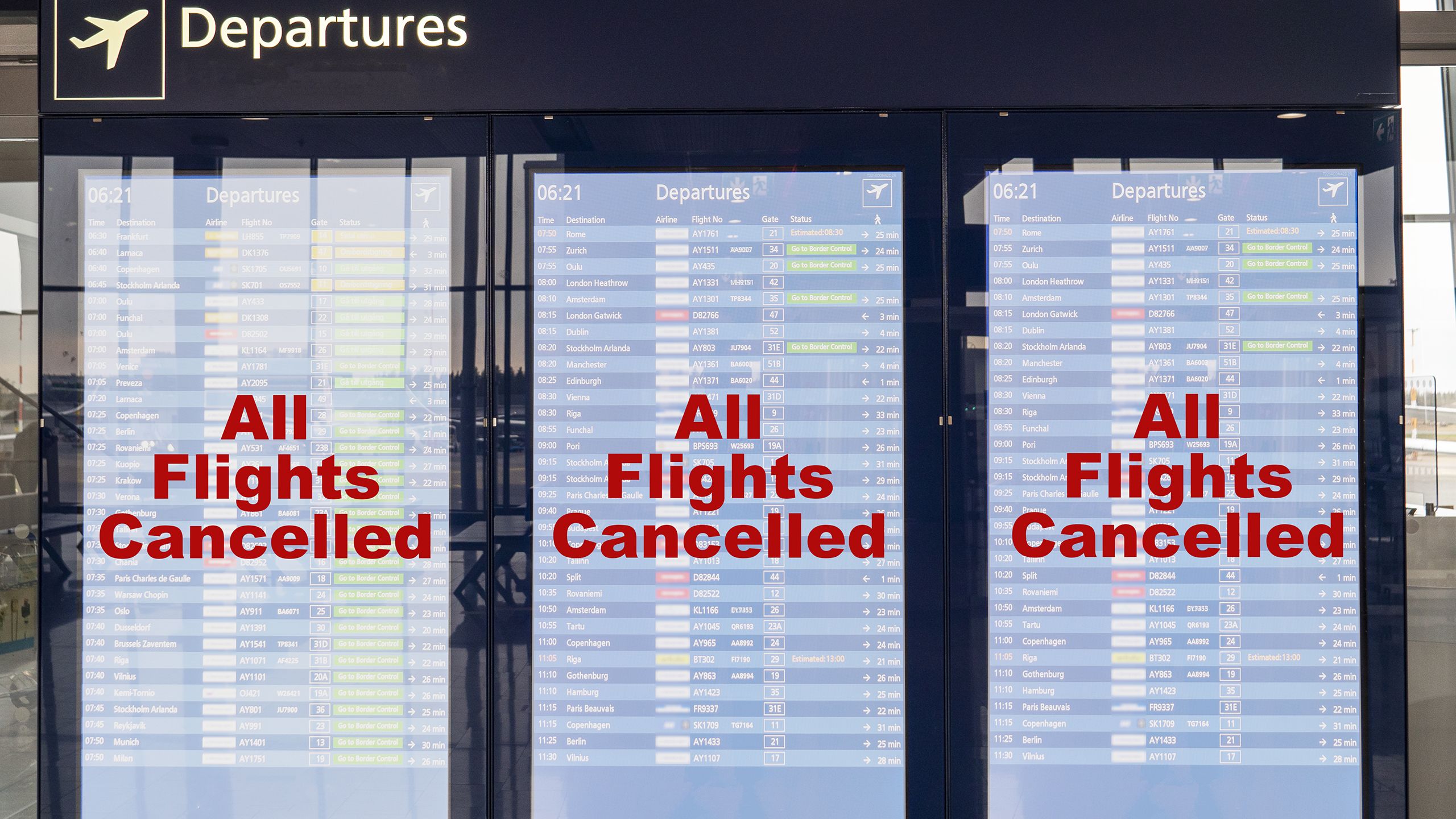
As well as designing and manufacturing aircraft, Boeing also provides its airline customers with a wide range of after-sales support, including planning and managing airline operations.
Professor Duncan McFarlane and his team at the Institute for Manufacturing have been working with Boeing for many years to analyse and manage disruptions.
Around eight years ago, the IfM team started to apply its expertise in disruption management and data analytics to address the complicated problem of airline scheduling, working in collaboration with both Boeing and its airline partners.
"Increasing efficiency by minimising disruption to schedules has an important role to play in reducing emissions," explains McFarlane. "We are working with Boeing and their airline customers to help them handle disruptions better and to understand why one flight can be delayed with very little knock-on effect to the schedules, but another creates airport mayhem."
To answer those questions, McFarlane's team has used machine learning to develop a software tool that looks at multiple data sources, works out what's causing the problems and which types of disruption are likely to have more severe consequence than others.
The software has already been used to analyse nearly 100,000 flights and, according to Goran Stojkovic, a Boeing Technical Fellow who works for Digital Aviation Solutions at Boeing Global Services, “it is helping us see what is really happening in the back-end so we can adjust flight schedules to minimise problems.”
How to go about minimising those problems is the second part of the puzzle. The team is working on a further piece of software to help airlines deal with delays by resetting their schedule for the rest of the day, reassigning crews, aircraft, flights and passengers in the most effective way, to ensure as many seats are occupied as possible.
“This has been a fruitful project for Boeing”, says Stojkovic, “and we have identified some clear opportunities for deployment which we are taking forward.”
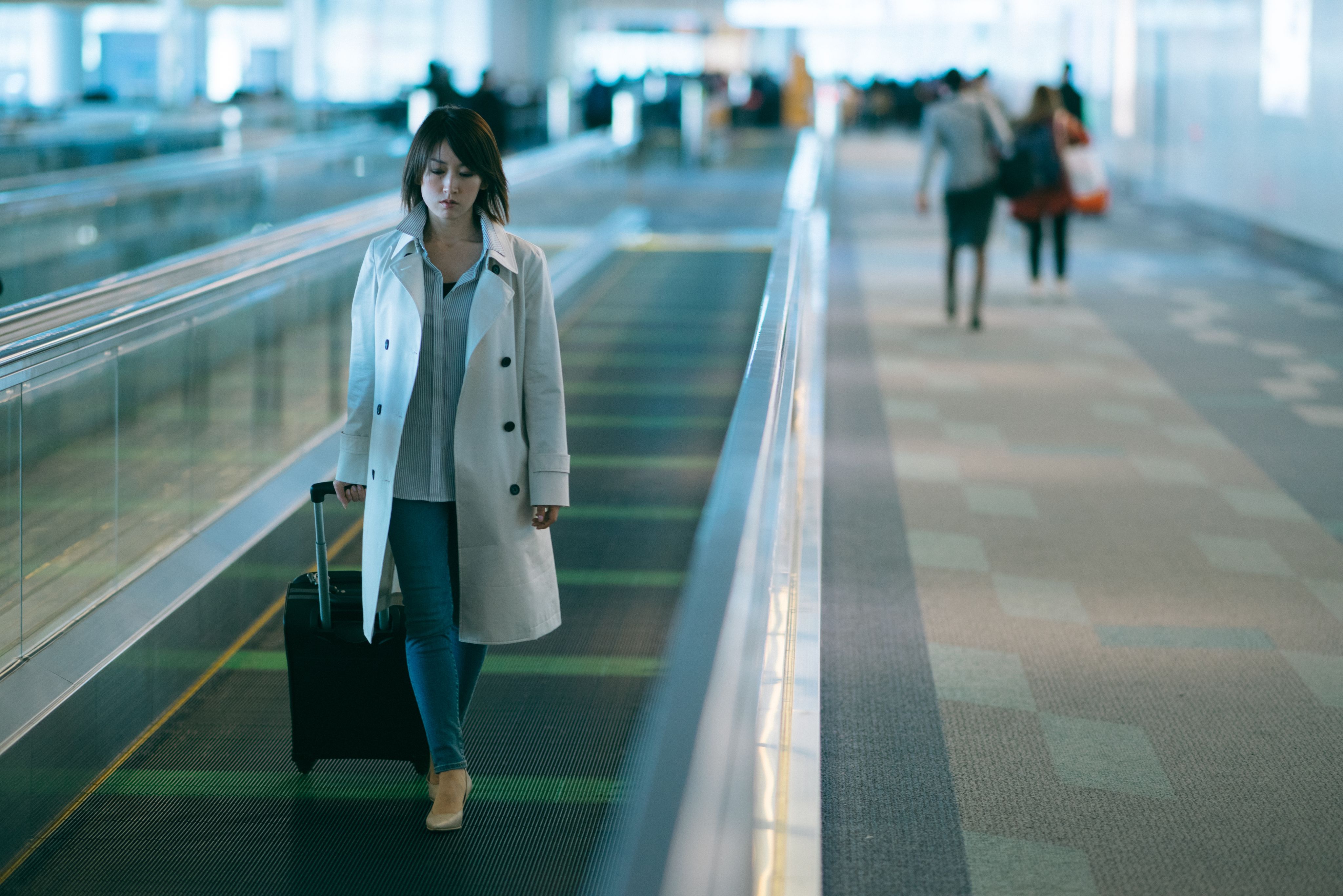
As Cambridge and Boeing celebrate 20 years of collaboration, Philip Guildford, Chief Operating Officer at the Department of Engineering and the University's partnership lead for Boeing, explains why the partnership has been so enduring and so valuable for both partners.
“Cambridge is a centre of world-class research and Boeing is a global industrial innovator. We both share a commitment to - and excitement about - the potential of fundamental science and the deployment of new technologies to have a positive effect on people's lives.
Never has that been more important than it is today, as we strive to accomplish this most complex but necessary of tasks: reimagining the future of aviation."
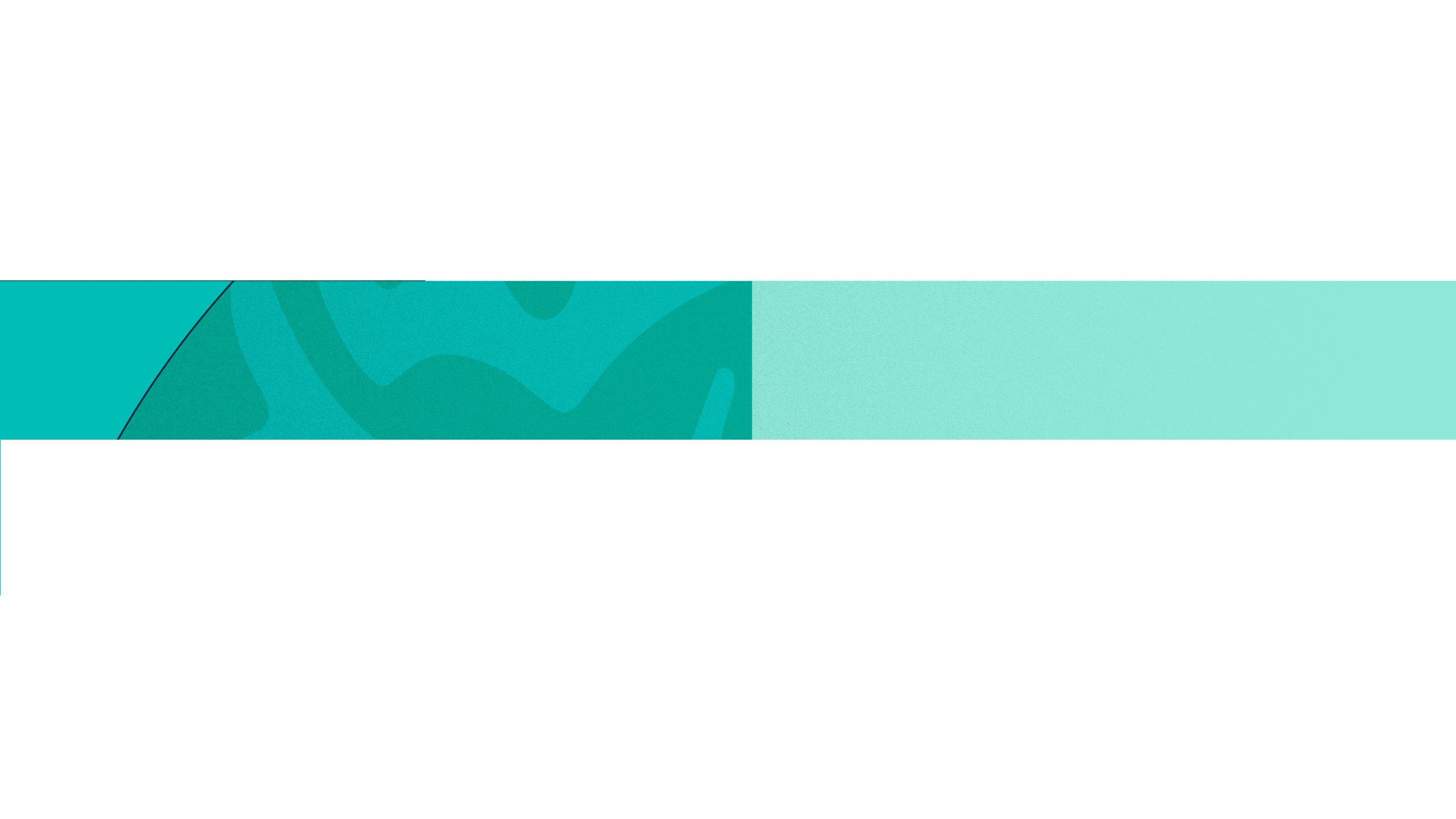
Published 16 February 2023
Photography
Dr Louisa Michael. Credit: Boeing
Boeing ecoDemonstrator in flight over mountains. Credit: Boeing. Photographer: PaulWeatherman
Hybrid-electric demonstrator: University of Cambridge
Iceberg shot from a drone. Getty Images. Credit: Carlo Cogni
Jet engine. Getty Images. Credit: Jonathan Knowles
Lightning bolt. Getty Images. Credit: Sarayut Thaneerat
Planes at gates. Getty Images. Credit: Michael H
Departure boards. Getty Images. Credit: Craig Hastings
Woman at airport. Getty Images. Credit: Benjamin Torode
The text in this work is licensed under a Creative Commons Attribution 4.0 International License