Online and Remote Engagement 2020
Professor Michael Ramage and team
Department of Architecture
School of Arts and Humanities
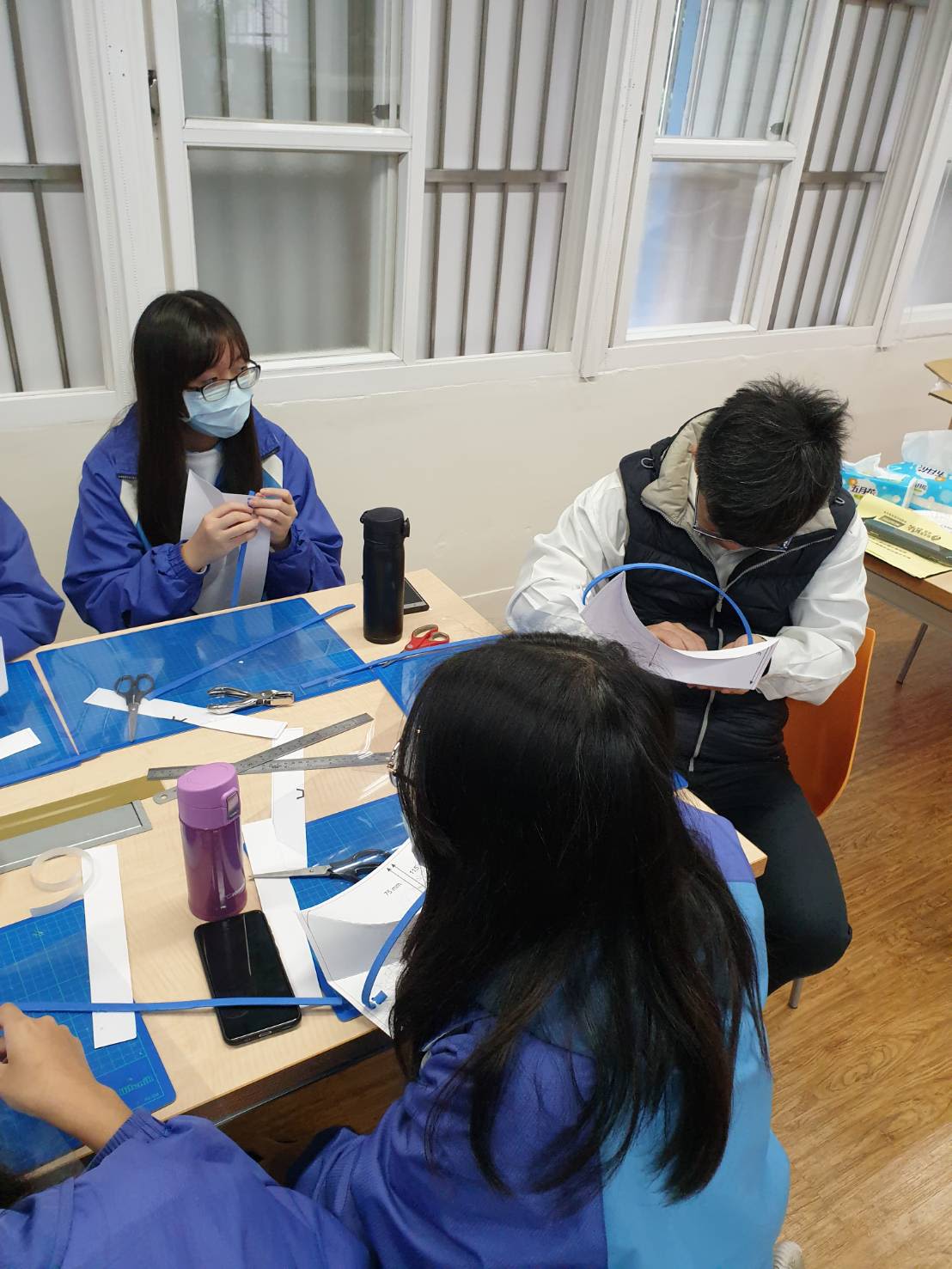
The Vice-Chancellor's Awards
for Research Impact and Engagement

About the researcher
Professor Michael Ramage is the Director of the Centre for Natural Material Innovation at Cambridge University. Trained as an architect and an engineer, he is a Reader in Architecture and Engineering in the Department of Architecture, a Fellow of Sidney Sussex College, and a founding partner of Light Earth Designs.
His current research is focused on developing low-energy structural materials and systems in masonry, better housing in the developing world and improved engineered timber and bamboo through natural material innovation.
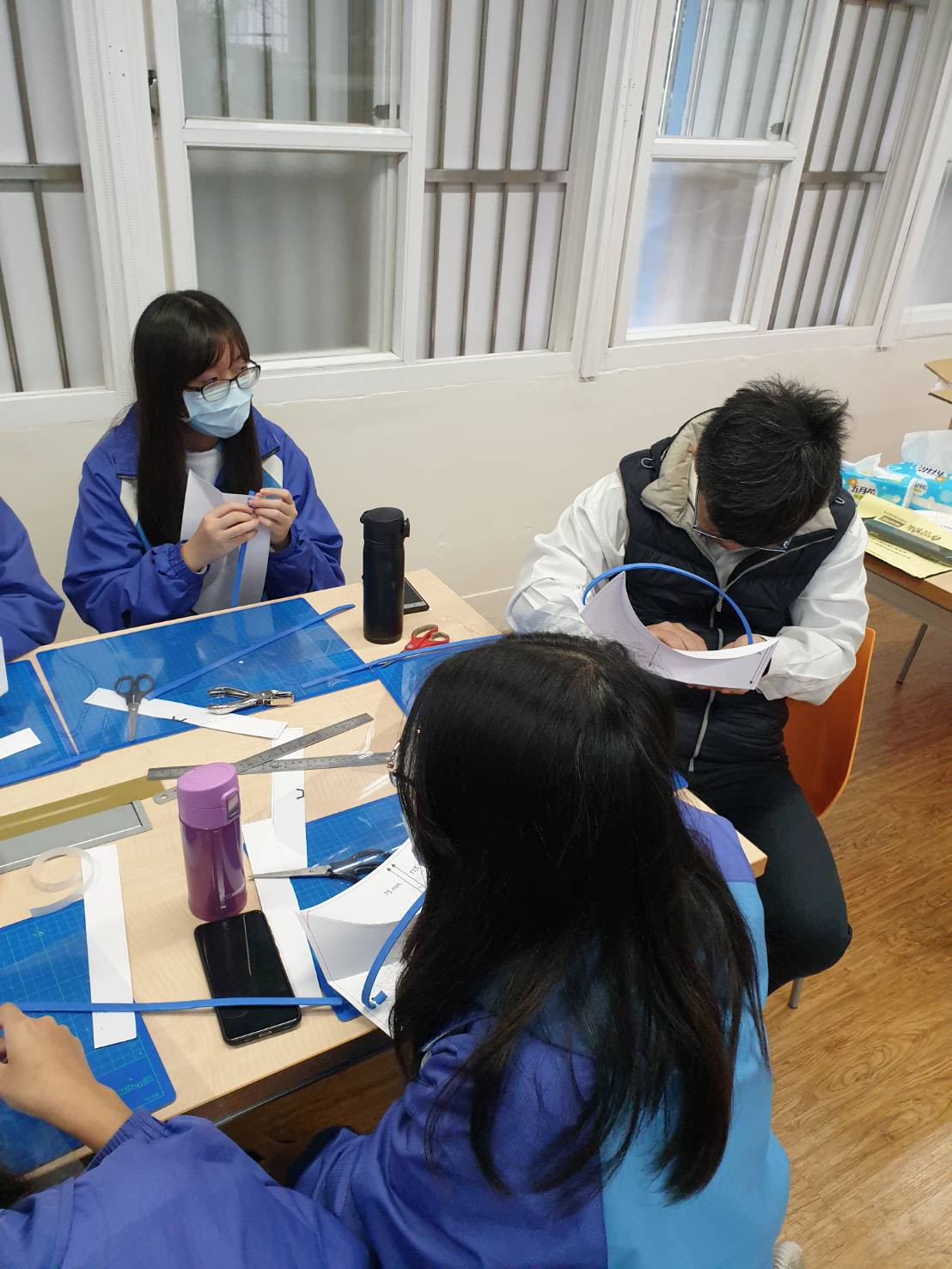
The Vice-Chancellor's Awards
for Research Impact and Engagement
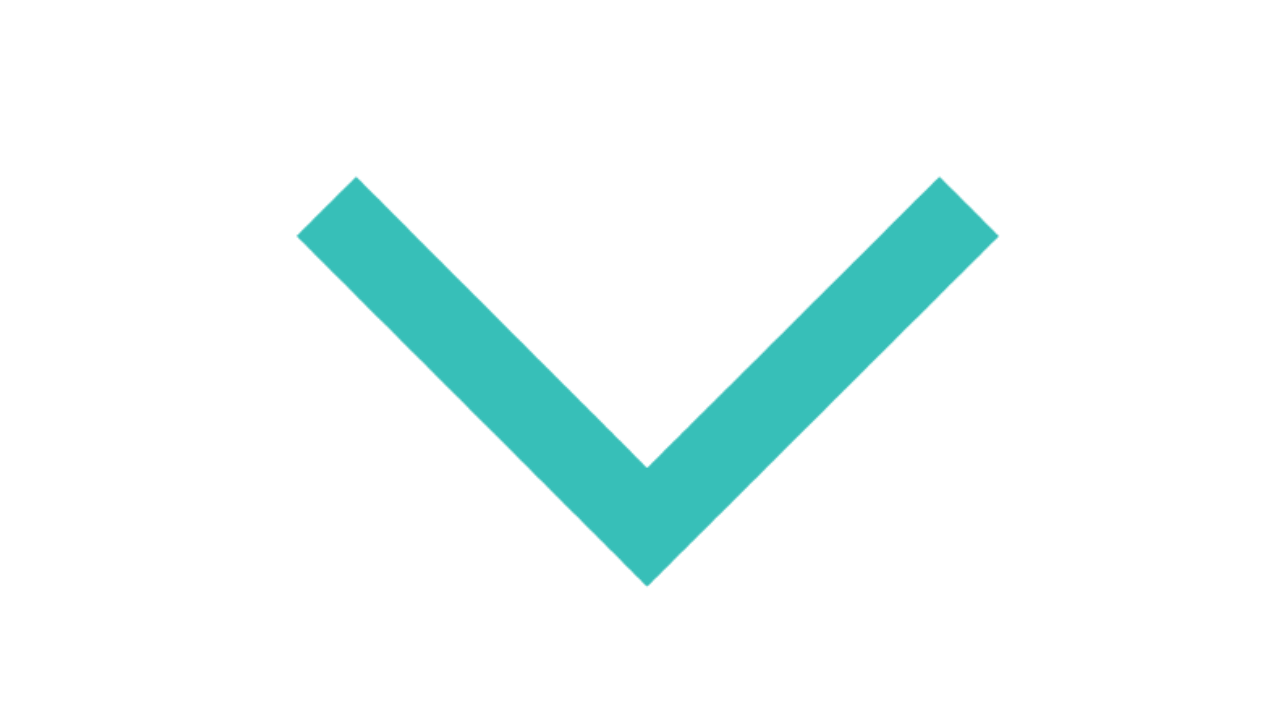
About the researcher
Professor Michael Ramage is the Director of the Centre for Natural Material Innovation at Cambridge University. Trained as an architect and an engineer, he is a Reader in Architecture and Engineering in the Department of Architecture, a Fellow of Sidney Sussex College, and a founding partner of Light Earth Designs.
His current research is focused on developing low-energy structural materials and systems in masonry, better housing in the developing world and improved engineered timber and bamboo through natural material innovation.
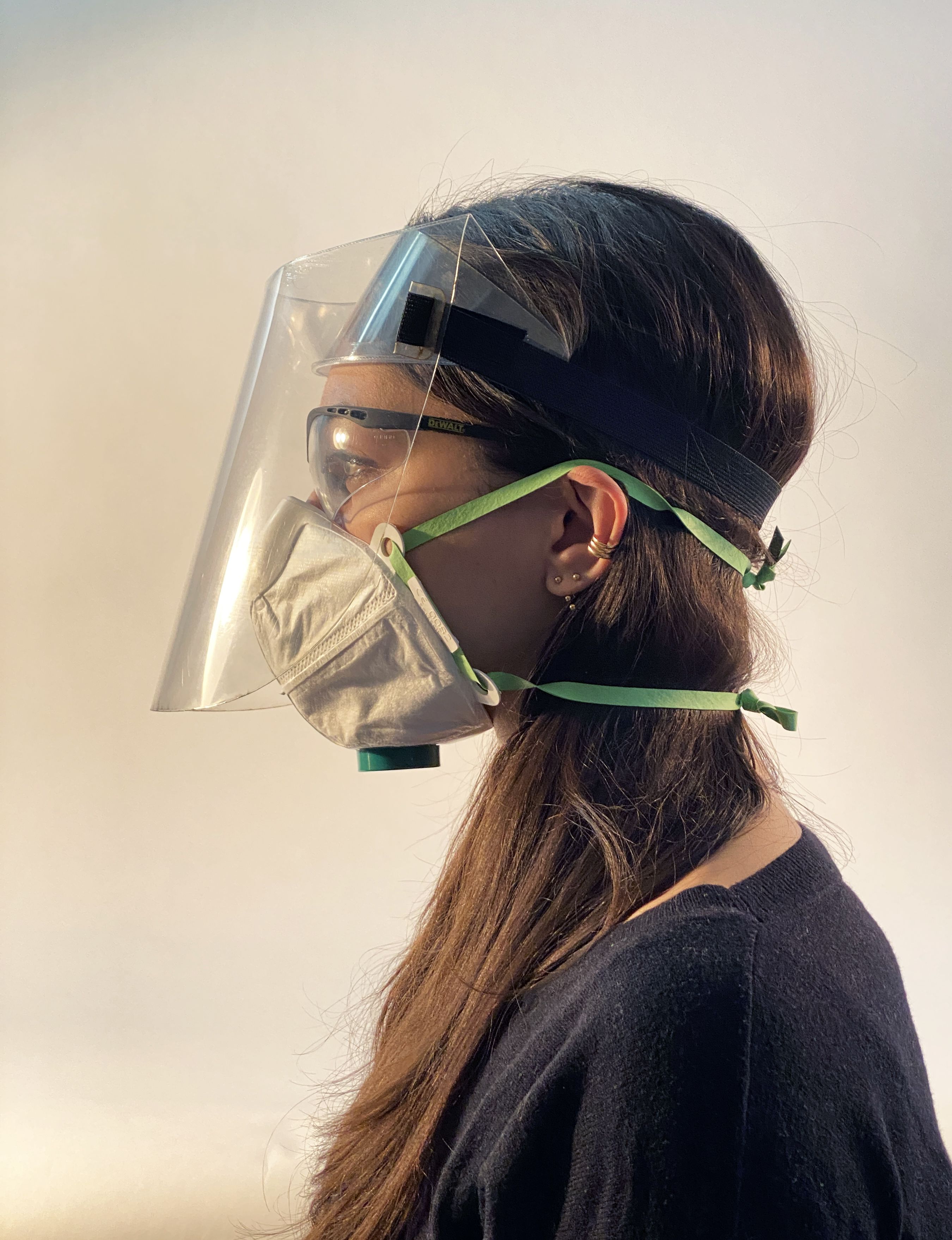
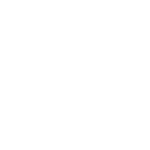
It's viable anywhere in the world, whatever your resources.
Michael Ramage in Deezen:
Simple origami face shield can be folded from single sheet of plastic (dezeen.com)
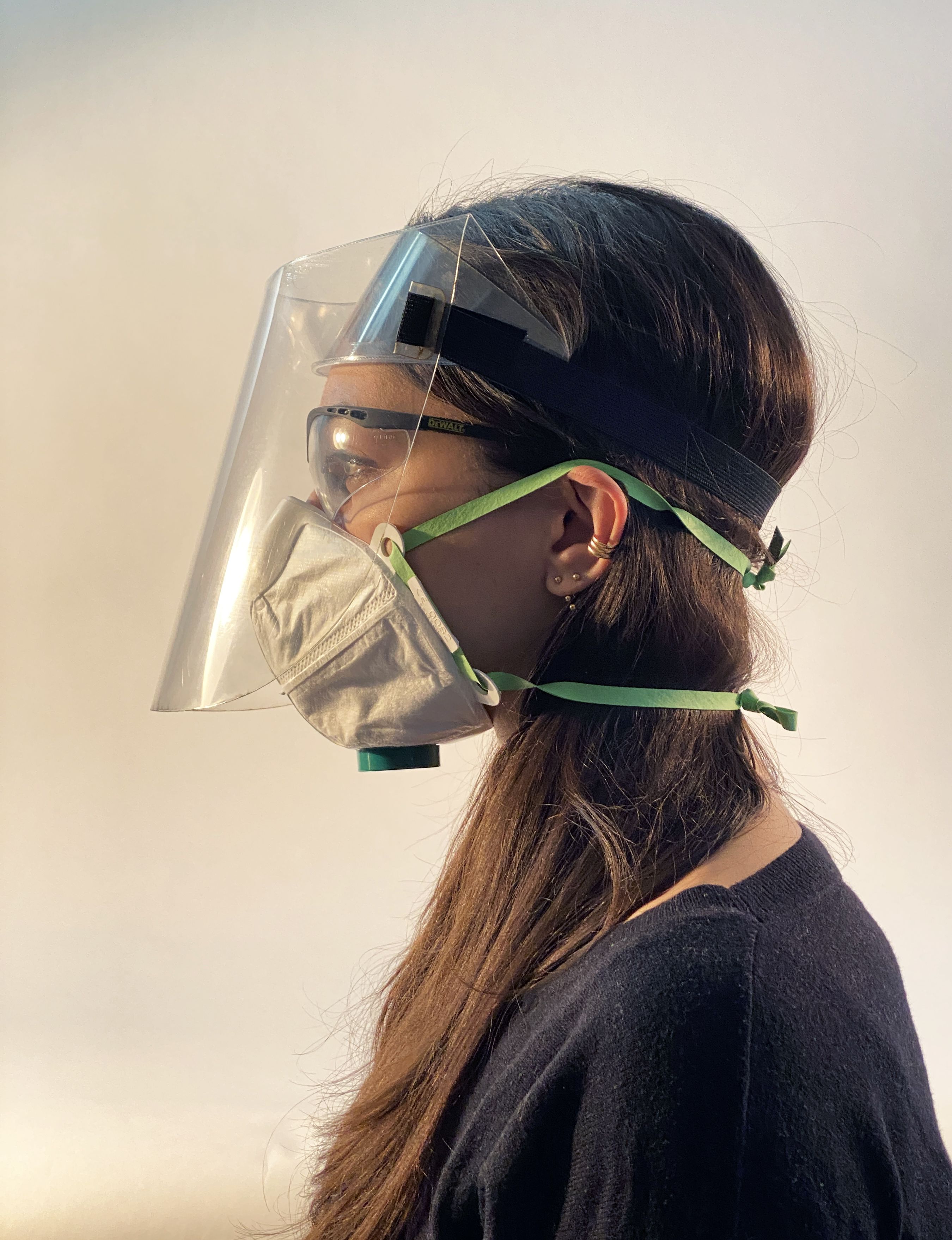
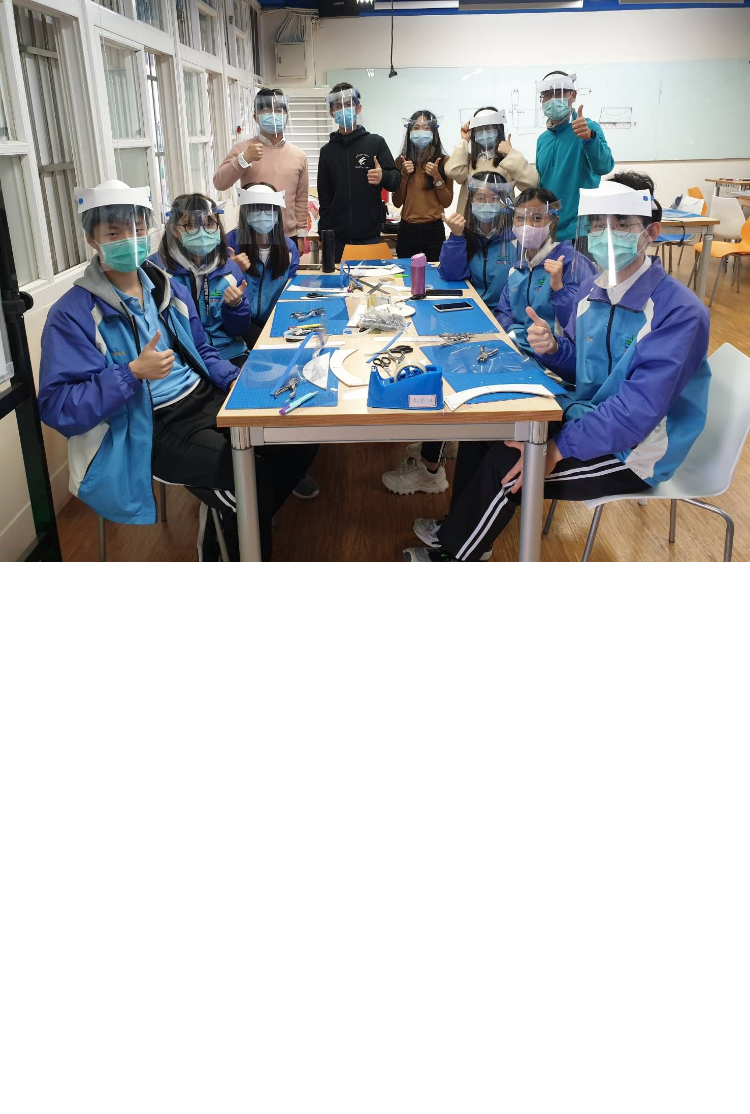
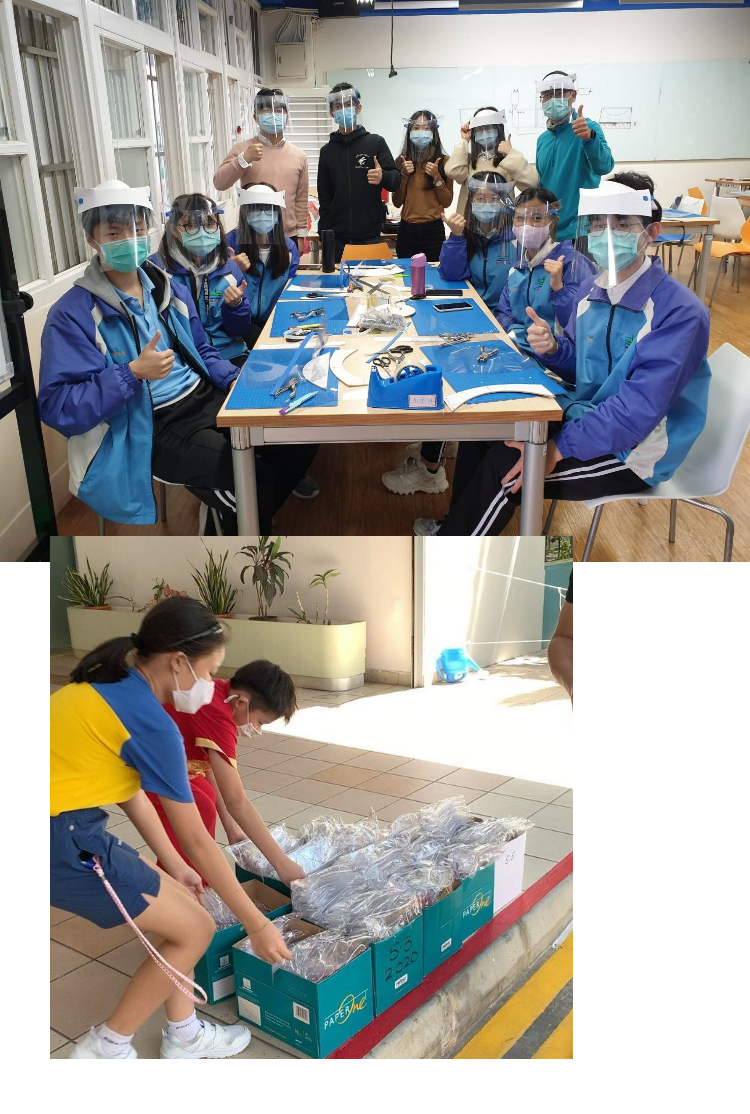
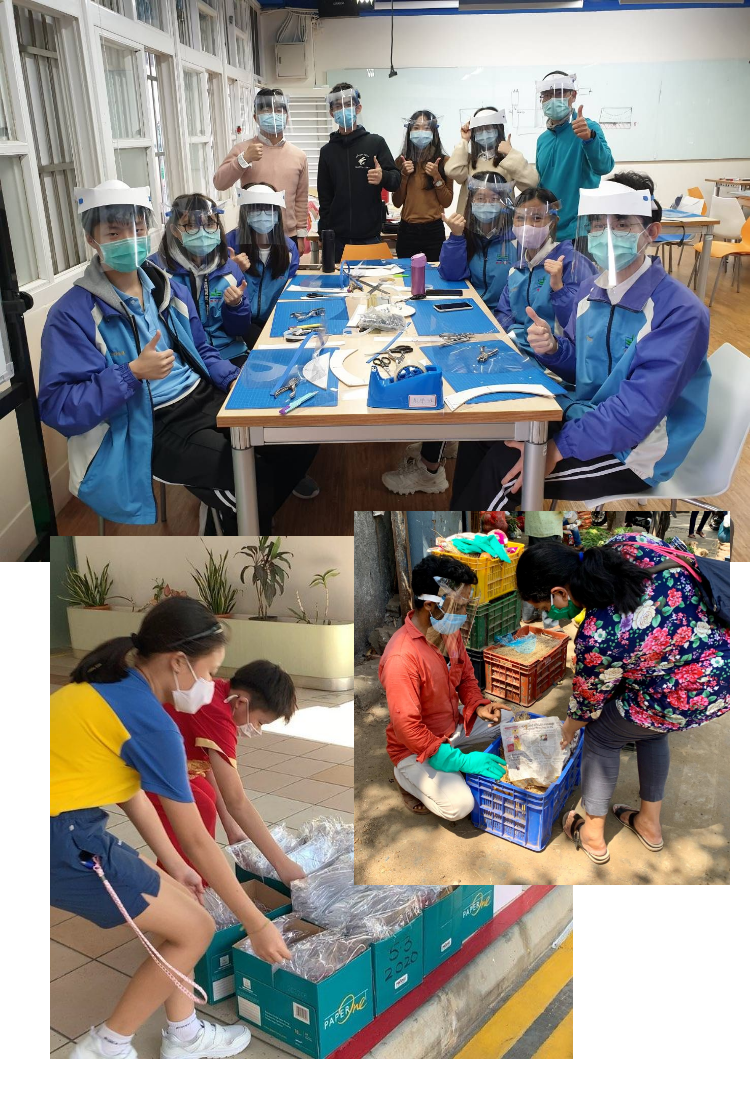
What is the research?
The HappyShield Project
Requiring nothing more than a pair of scissors, a ruler and a ballpoint pen, Professor Ramage and his team developed, tested and disseminated a novel open-source medical face shield design in response to the severe personal protective equipment (PPE) shortages caused by the COVID-19 pandemic.
A preliminary survey of existing medical face shield designs identified a number of key challenges: slow manufacturing rates, non-reusability, poor packing efficiency, and limitations in adapting designs to local requirements and available materials and manufacturing methods.
The focus of the HappyShield project has been the development of a design enabling cost-effective, scalable and flexible production with a particular emphasis on manufacturing and distribution in Low and Middle Income Countries (LMIC’s).
The team launched a website which freely shares their cutting and folding templates, together with practical pictorial and video instructions. The face shield design has obtained CE Marking certification through the British Standards Institute as approved PPE for the UK and EU.
To ensure the ability for other designers to use our design and adapt it as needed to their local context, we published these materials under the Creative Commons Attribution NonCommercial- ShareAlike 4.0 International license.
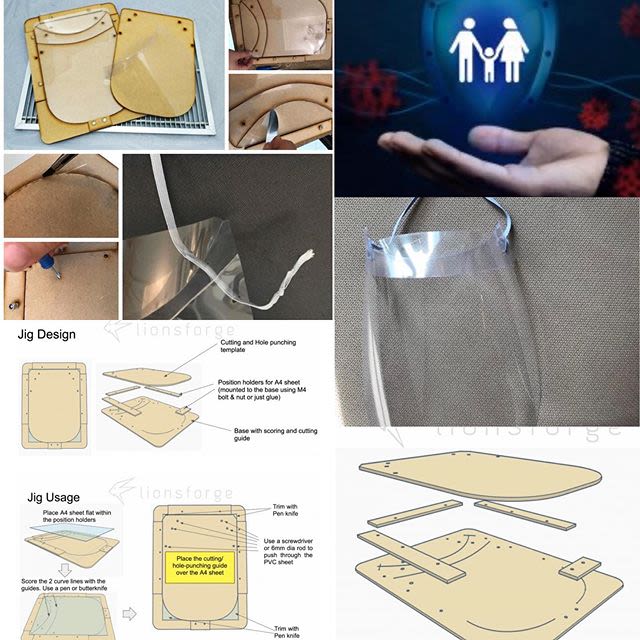
The effectiveness of this dissemination strategy has been demonstrated by the large number of designers, manufacturers and academics globally, including in South Africa, India, Chile, Colombia, Brazil, Taiwan, Singapore, the UK and the USA who have reached out to us to share their own adaptations of the design or to explore collaboration opportunities.
As evidence of the real-world impact of this approach, an independent maker group in Singapore reported the production and distribution of several thousand shields based on HappyShield to front-line workers there just weeks after the design was first publicised.
Confirming our hypotheses regarding the low real-world cost of our design, this group reported costs of approximately S$0.13 per shield, approximately 1/6 of the WHO’s estimate of USD$0.60 per face shield.
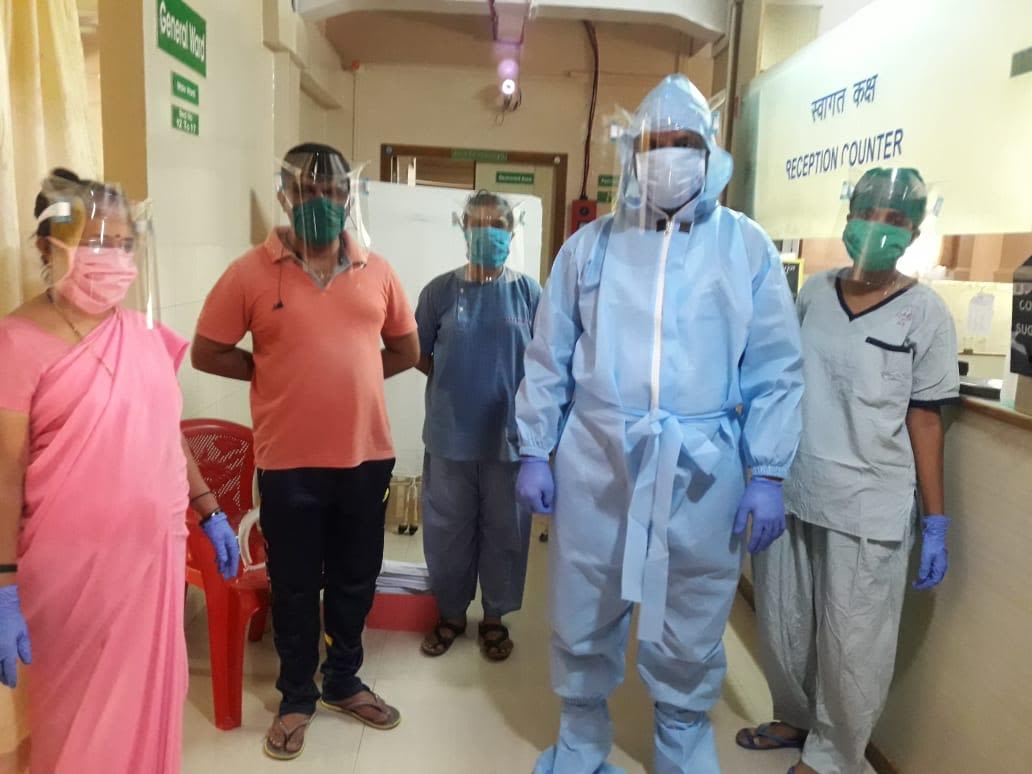
Illustration
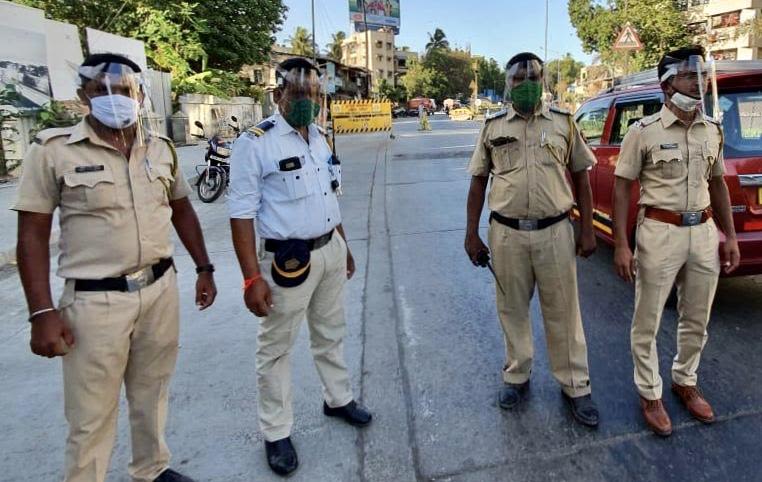
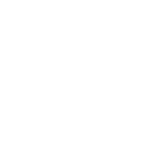
A really strong application that demonstrated rapid, effective response to COVID19. Conducting the work for clearly defined publics from the outset.
The judges
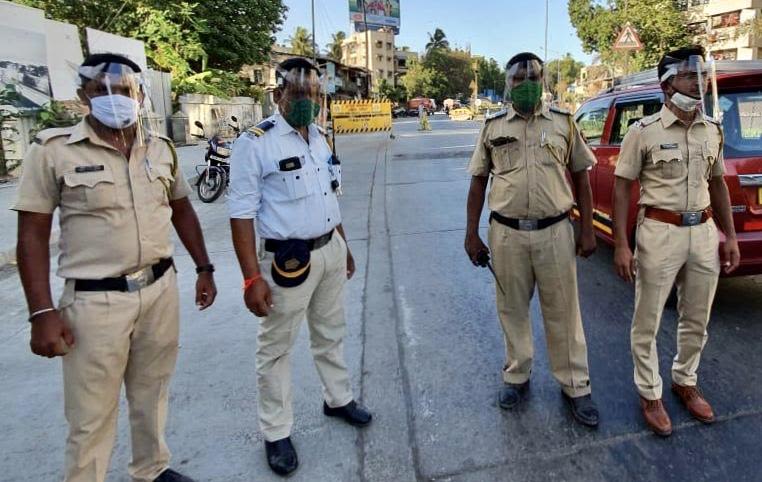
Future of the research
In addition to the HappyShield design being taken up and adapted by independent makers in Taiwan, Singapore, India, and the US, a number of research collaborations have also begun as a result of engagement.
The team are currently pursuing UKRI Global Challenges Research Funding with University of Cambridge Institute for Manufacturing and academics at the University of Bath for future research aimed at developing improved open source hardware documentation and testing methodologies in LMIC’s, to be evaluated through pilot projects in Ethiopia and Malawi.
The team are currently translating their instructions into as many as ten languages, whose speakers cumulatively comprise roughly a third of the global population.
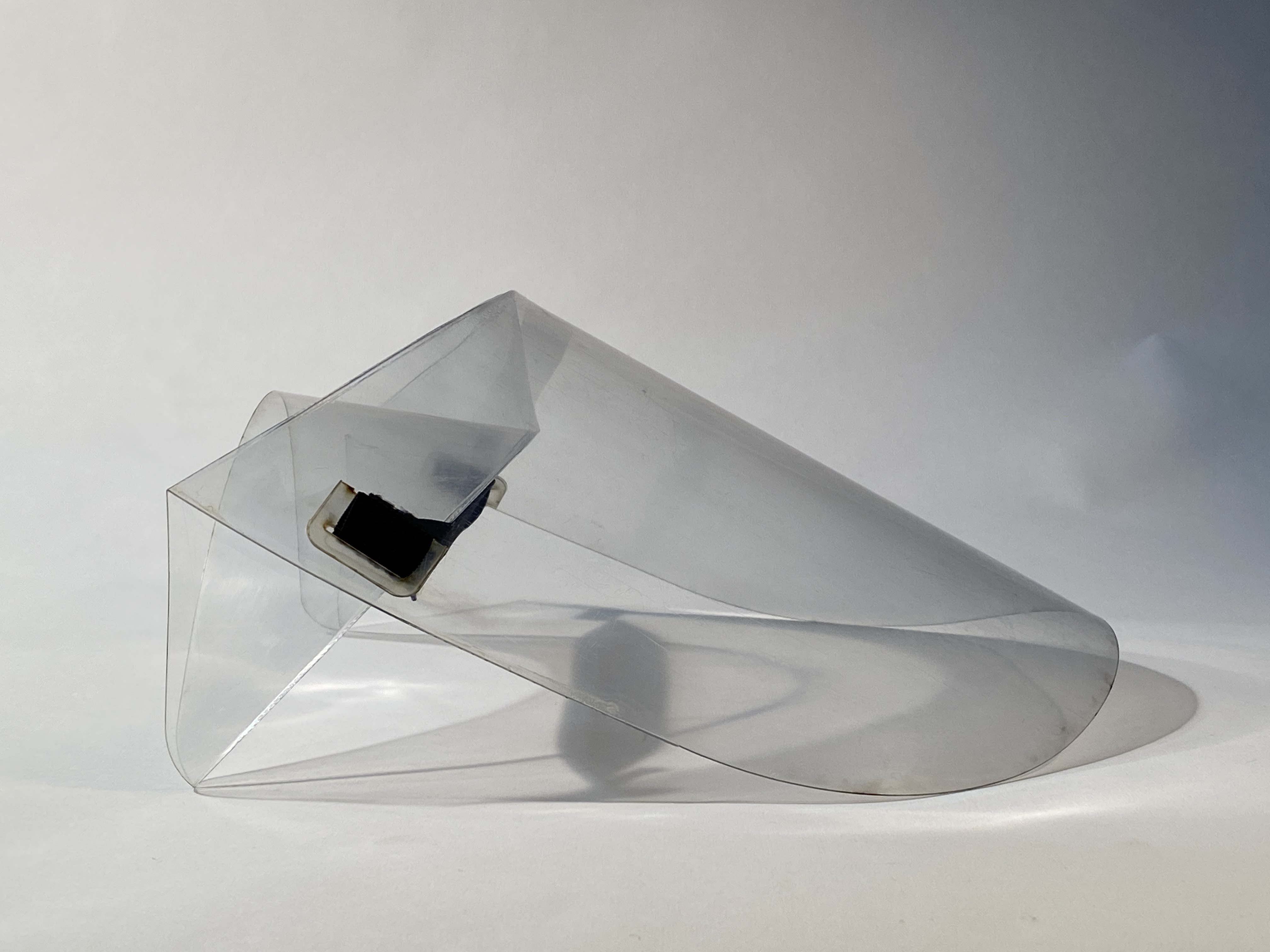